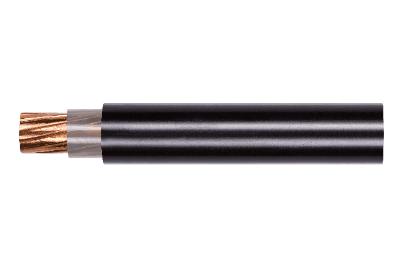
Polyethylene (PE) is widely used in the insulation and sheathing of power cables and telecommunication cables due to its excellent mechanical strength, toughness, heat resistance, insulation, and chemical stability. However, due to the structural characteristics of PE itself, its resistance to environmental stress cracking is relatively poor. This issue becomes particularly prominent when PE is used as the outer sheath of large-section armored cables.
1. Mechanism of PE Sheath Cracking
PE sheath cracking mainly occurs in two situations:
a. Environmental Stress Cracking: This refers to the phenomenon where the sheath undergoes brittle cracking from the surface due to combined stress or exposure to environmental media after cable installation and operation. It's primarily caused by internal stress within the sheath and prolonged exposure to polar liquids. Extensive research on material modification has substantially resolved this type of cracking.
b. Mechanical Stress Cracking: This occurs due to structural deficiencies in the cable or inappropriate sheath extrusion processes, leading to significant stress concentration and deformation-induced cracking during cable installation. This type of cracking is more pronounced in the outer sheaths of large-section steel tape armored cables.
2. Causes of PE Sheath Cracking and Improvement Measures
2.1 Influence of Cable Steel Tape Structure
In cables with larger outer diameters, the armored layer is typically composed of double-layer steel tape wraps. Depending on the cable's outer diameter, the steel tape thickness varies (0.2mm, 0.5mm, and 0.8mm). Thicker armored steel tapes have higher rigidity and poorer plasticity, resulting in greater spacing between upper and lower layers. During extrusion, this causes significant differences in sheath thickness between the upper and lower layers of the armored layer's surface. Thinner sheath areas at the edges of the outer steel tape experience the greatest stress concentration and are the primary areas where future cracking occurs.
To mitigate the impact of the armored steel tape on the outer sheath, a buffering layer of a certain thickness is wrapped or extruded between the steel tape and the PE sheath. This buffering layer should be uniformly dense, without wrinkles or protrusions. The addition of a buffering layer improves the smoothness between the two layers of steel tape, ensures uniform PE sheath thickness, and, combined with the contraction of the PE sheath, reduces internal stress.
ONEWORLD provides users with different thicknesses of galvanized steel tape armored materials to meet diverse needs.
2.2 Impact of Cable Production Process
The primary issues with the extrusion process of large outer diameter armored cable sheaths are inadequate cooling, improper mold preparation, and excessive stretching ratio, resulting in excessive internal stress within the sheath. Large-sized cables, due to their thick and wide sheaths, often face limitations in the length and volume of water troughs on extrusion production lines. Cooling down from over 200 degrees Celsius during extrusion to room temperature poses challenges. Inadequate cooling leads to a softer sheath near the armor layer, causing scratching on the sheath's surface when the cable is coiled, eventually resulting in potential cracks and breakage during cable laying due to external forces. Moreover, insufficient cooling contributes to increased internal shrinkage forces after coiling, elevating the risk of sheath cracking under substantial external forces. To ensure sufficient cooling, increasing the length or volume of water troughs is recommended. Lowering the extrusion speed while maintaining proper sheath plasticization and allowing ample time for cooling during coiling is essential. Additionally, considering polyethylene as a crystalline polymer, a segmented temperature reduction cooling method, from 70-75°C to 50-55°C, and finally to room temperature, helps alleviate internal stresses during the cooling process.
2.3 Influence of Coiling Radius on Cable Coiling
During cable coiling, manufacturers adhere to industry standards for selecting appropriate delivery reels. However, accommodating lengthy delivery lengths for large outer diameter cables poses challenges in selecting suitable reels. To meet specified delivery lengths, some manufacturers reduce reel barrel diameters, resulting in insufficient bending radii for the cable. Excessive bending leads to displacement in armor layers, causing significant shearing forces on the sheath. In severe cases, the armored steel strip's burrs can pierce the cushioning layer, embedding directly into the sheath and causing cracks or fissures along the edge of the steel strip. During cable laying, the lateral bending and pulling forces cause the sheath to crack along these fissures, especially for cables closer to the reel's inner layers, making them more prone to breakage.
2.4 Impact of On-site Construction and Installation Environment
To standardize cable construction, it is advised to minimize the cable laying speed, avoiding excessive lateral pressure, bending, pulling forces, and surface collisions, ensuring a civilized construction environment. Preferably, before cable installation, allow the cable to rest at 50-60°C to release internal stress from the sheath. Avoid prolonged exposure of cables to direct sunlight, as differential temperatures on various sides of the cable may lead to stress concentration, increasing the risk of sheath cracking during cable laying.
Post time: Dec-18-2023