In recent years, the usage of fire-resistant cables has been on the rise. This surge is primarily due to users acknowledging the performance of these cables. Consequently, the number of manufacturers producing these cables has also increased. Ensuring the long-term stability and quality of fire-resistant cables is of paramount importance.
Typically, some companies first produce a trial batch of fire-resistant cable products and send them for inspection to relevant national detection agencies. After obtaining detection reports, they proceed with mass production. However, a few cable manufacturers have established their own fire resistance testing laboratories. The fire resistance test serves as an examination of the production process's cable-making results. The same production process may yield cables with slight performance differences at different times. For cable manufacturers, if the pass rate of fire resistance tests for fire-resistant cables is 99%, there remains a 1% safety hazard. This 1% risk for users translates into 100% danger. To address these issues, the following discusses how to improve the pass rate of fire-resistant cable fire resistance tests from aspects like raw materials, conductor selection, and production process control:
1. Use of Copper Conductors
Some manufacturers use copper-clad aluminum conductors as cable conductor cores. However, for fire-resistant cables, copper conductors should be chosen instead of copper-clad aluminum conductors.
2. Preference for Round Compact Conductors
For circular conductor cores with axial symmetry, the mica tape wrapping is tight in all directions after wrapping. Therefore, for the conductor structure of fire-resistant cables, it is preferable to use round compact conductors.
The reasons being: Some users prefer conductor structures with a stranded soft structure, which requires enterprises to communicate with users about changing to round compact conductors for reliability in cable usage. A soft stranded structure or double twisting easily causes damage to the mica tape, making it unsuitable for fire-resistant cable conductors. However, some manufacturers believe that they should meet the users' requirements for fire-resistant cables, without fully understanding the relevant details. Cables are closely related to human life, so cable manufacturing enterprises must clearly explain the relevant technical issues to users.
Fan-shaped conductors are also not advisable because the pressure distribution on the mica tape wrapping of fan-shaped conductors is uneven, making them prone to scratching and collisions, thereby reducing electrical performance. Additionally, from a cost perspective, the sectional perimeter of a fan-shaped conductor structure is larger than that of a circular conductor, increasing the consumption of expensive mica tape. Although the outer diameter of a circular structured cable increases, and there is an increased use of PVC sheath material, in terms of overall cost, circular structure cables are still more cost-effective. Therefore, based on the above analysis, from both technical and economic perspectives, the adoption of a circular structured conductor is preferable for fire-resistant power cables.
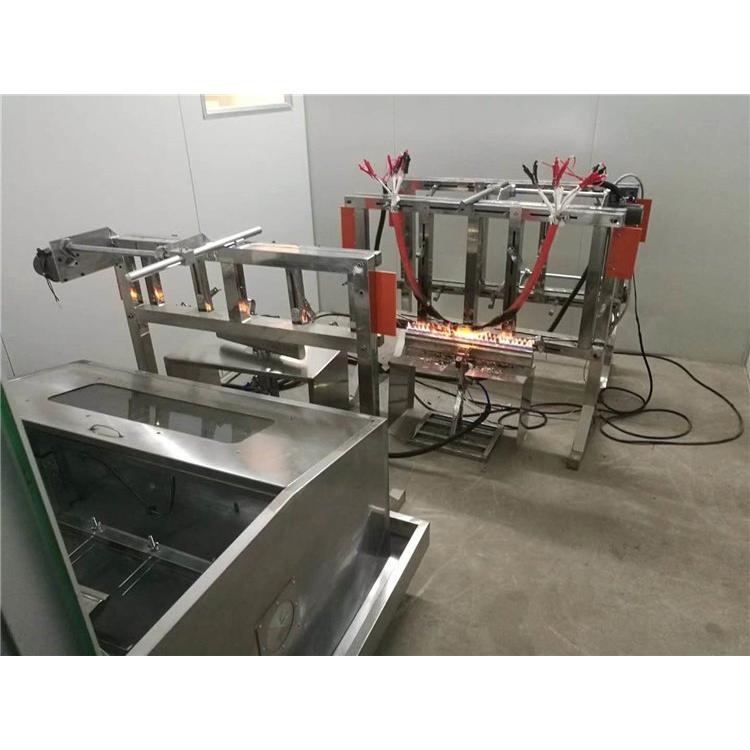
Post time: Dec-07-2023