The metal shielding layer is an indispensable structure in medium-voltage(3.6/6kV∽26/35kV) cross-linked polyethylene-insulated power cables. Properly designing the structure of the metal shield, accurately calculating the short-circuit current the shield will bear, and developing a reasonable shield processing technique are vital for ensuring the quality of cross-linked cables and the safety of the entire operating system.
Shielding Process:
The shielding process in medium-voltage cable production is relatively simple. However, if attention is not paid to certain details, it can lead to severe consequences for cable quality.
1. Copper Tape Shielding Process:
The copper tape used for shielding must be fully annealed soft copper tape without defects like curled edges or cracks on both sides. Copper tape that is too hard can damage the semiconductive layer, while tape that is too soft may wrinkle easily. During wrapping, it's essential to set the wrapping angle correctly, control the tension properly to avoid over-tightening. When cables are energized, insulation generates heat and expands slightly. If the copper tape is wrapped too tightly, it may embed into the insulating shield or cause the tape to break. Soft materials should be used as padding on both sides of the shielding machine's take-up reel to prevent any possible damage to the copper tape during the subsequent steps in the process. Copper tape joints should be spot-welded, not soldered, and certainly not connected using plugs, adhesive tapes, or other non-standard methods.
In the case of copper tape shielding, contact with the semiconductive layer can result in oxide formation due to the contact surface, reducing contact pressure and doubling contact resistance when the metal shielding layer undergoes thermal expansion or contraction and bending. Poor contact and thermal expansion may lead to direct damage to the external semiconductive layer. Proper contact between the copper tape and the semiconductive layer is essential to ensure effective grounding. Overheating, as a result of thermal expansion, may cause the copper tape to expand and deform, damaging the semiconductive layer. In such cases, the poorly connected or improperly welded copper tape can carry a charging current from the non-grounded end to the grounded end, leading to overheating and rapid aging of the semiconductive layer at the point of the copper tape's breakage.
2. Copper Wire Shielding Process:
When employing loosely wound copper wire shielding, wrapping the copper wires directly around the outer shield surface can easily cause tight wrapping, potentially damaging the insulation and leading to cable breakdown. To address this, it's necessary to add 1-2 layers of semiconductive nylon tape around the extruded semiconductive outer shield layer after extrusion.
Cables using loosely wound copper wire shielding do not suffer from oxide formation found between copper tape layers. Copper wire shielding has minimal bending, little thermal expansion deformation, and a smaller increase in contact resistance, all of which contribute to improved electrical, mechanical, and thermal performance in cable operation.
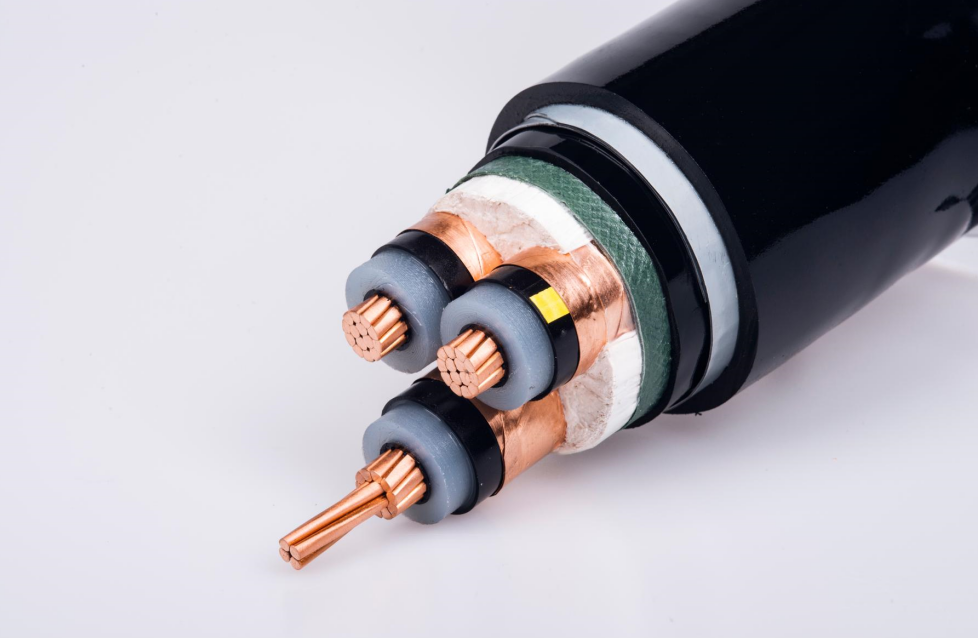
Post time: Oct-27-2023