Abstract: The cross-linking principle, classification, formulation, process and equipment of silane cross-linked polyethylene insulating material for wire and cable are briefly described, and some characteristics of silane naturally cross-linked polyethylene insulating material in application and use as well as factors affecting the cross-linking condition of the material are introduced.
Keywords: Silane cross-linking; Natural cross-linking; Polyethylene; Insulation; Wire and cable
Silane cross-linked polyethylene cable material is now widely used in the wire and cable industry as an insulating material for low-voltage power cables. The material in the manufacture of cross-linked wire and cable, and peroxide cross-linking and irradiation cross-linking compared with the manufacturing equipment required is simple, easy to operate, low comprehensive cost and other advantages, has become the leading material for low-voltage cross-linked cable with insulation.
1.Silane cross-linked cable material cross-linking principle
There are two main processes involved in making silane cross-linked polyethylene: grafting and cross-linking. In the grafting process, the polymer loses its H-atom on the tertiary carbon atom under the action of free initiator and pyrolysis into free radicals, which react with the – CH = CH2 group of vinyl silane to produce a grafted polymer containing a trioxysilyl ester group. In the cross-linking process, the graft polymer is first hydrolysed in the presence of water to produce silanol, and the – OH condenses with the adjacent Si-O-H group to form the Si-O-Si bond, thus cross-linking the polymer macromolecules.
2.Silane cross-linked cable material and its cable production method
As you know, there are two-step and one-step production methods for silane cross-linked cables and their cables. The difference between the two-step method and the one-step method lies in where the silane grafting process is carried out, the grafting process at the cable material manufacturer for the two-step method, the grafting process in the cable manufacturing plant for the one-step method. The two-step silane cross-linked polyethylene insulating material with the largest market share is composed of the so-called A and B materials, with A material being the polyethylene grafted with silane and B material being the catalyst master batch. The insulating core is then cross-linked in warm water or steam.
There is another type of two-step silane cross-linked polyethylene insulator, where the A material is produced in a different way, by introducing vinyl silane directly into the polyethylene during synthesis to obtain polyethylene with silane branched chains.
One-step method also has two types, the traditional one-step process is a variety of raw materials according to the formula in the ratio of special precision metering system, into a specially designed special extruder in one step to complete the grafting and extrusion of cable insulation core, in this process, no granulation, no need for cable material plant participation, by the cable factory to complete alone. This one-step silane cross-linked cable production equipment and formulation technology is mostly imported from abroad and is expensive.
Another type of one-step silane cross-linked polyethylene insulation material is produced by cable material manufacturers, is all raw materials according to the formula in the ratio of a special method of mixing together, packaged and sold, there is no A material and B material, cable plant can be directly in the extruder to complete a step at the same time grafting and extrusion of cable insulation core. The unique feature of this method is that there is no need for expensive special extruders, as the silane grafting process can be completed in an ordinary PVC extruder, and the two-step method eliminates the need to mix A and B materials before extrusion.
3. Formulation composition
The formulation of silane cross-linked polyethylene cable material is generally composed of base material resin, initiator, silane, antioxidant, polymerization inhibitor, catalyst, etc.
(1) The base resin is generally a low density polyethylene (LDPE) resin with a melt index (MI) of 2, but recently, with the development of synthetic resin technology and cost pressures, linear low density polyethylene (LLDPE) has also been used or partially used as the base resin for this material. Different resins often have a significant impact on grafting and cross-linking due to differences in their internal macromolecular structure, so the formulation will be modified by using different base resins or the same type of resin from different manufacturers.
(2) The initiator commonly used is diisopropyl peroxide (DCP), the key is to grasp the amount of the problem, too little to cause silane grafting is not enough; too much to cause polyethylene cross-linking, which reduces its fluidity, the surface of the extruded insulation core rough, difficult to squeeze system. As the amount of initiator added is very small and sensitive, it is important to disperse it evenly, so it is generally added together with the silane.
(3) Silane is generally used vinyl unsaturated silane, including vinyl trimethoxysilane (A2171) and vinyl triethoxysilane (A2151), due to the fast hydrolysis rate of A2171, so choose A2171 more people. Similarly, there is a problem of adding silane, the current cable material manufacturers are trying to achieve its lower limit to reduce costs, because the silane are imported, the price is more expensive.
(4) Anti-oxidant is to ensure the stability of polyethylene processing and cable anti-aging and added, anti-oxidant in the silane grafting process has the role of inhibiting the grafting reaction, so the grafting process, the addition of anti-oxidant to be careful, the amount added to consider the amount of DCP to match the selection. In the two-step cross-linking process, most of the antioxidant can be added in the catalyst master batch, which can reduce the impact on the grafting process. In the one-step cross-linking process, the antioxidant is present in the entire grafting process, so the choice of species and amount is more important. Commonly used antioxidants are 1010, 168, 330, etc.
(5) Polymerization inhibitor is added in order to inhibit some grafting and cross-linking process of side reactions occur, in the grafting process to add an anti-cross-linking agent, can effectively reduce the occurrence of C2C cross-linking, thereby improving the processing fluidity, in addition, the addition of a graft in the same conditions will be preceded by the hydrolysis of silane on the polymerization inhibitor can reduce the hydrolysis of grafted polyethylene, to improve the long-term stability of the graft material.
(6) Catalysts are often organotin derivatives (except for natural crosslinking), the most common being dibutyltin dilaurate (DBDTL), which is generally added in the form of a masterbatch. In the two-step process, the graft (A material) and the catalyst master batch (B material) are packaged separately and the A and B materials are mixed together before being added to the extruder to prevent pre-crosslinking of the A material. In the case of one-step silane cross-linked polyethylene insulations, the polyethylene in the package has not yet been grafted, so there is no pre-cross-linking problem and therefore the catalyst does not need to be packaged separately.
In addition, there are compounded silanes available on the market, which are a combination of silane, initiator, antioxidant, some lubricants and anti-copper agents, and are generally used in one-step silane cross-linking methods in cable plants.
Therefore, the formulation of silane cross-linked polyethylene insulation, the composition of which is not considered to be very complex and is available in the relevant information, but the appropriate production formulations, subject to some adjustments in order to finalise, which requires a full understanding of the role of the components in the formulation and the law of their impact on performance and their mutual influence.
In the many varieties of cable materials, silane cross-linked cable material (either two-step or one-step) is considered to be the only variety of chemical processes occurring in extrusion, other varieties such as polyvinyl chloride (PVC) cable material and polyethylene (PE) cable material, the extrusion granulation process is a physical mixing process, even if the chemical cross-linking and irradiation cross-linking cable material, whether in the extrusion granulation process, or extrusion system Cable, there is no chemical process occurs, so, in comparison, the production of silane cross-linked cable material and cable insulation extrusion, process control is more important.
4. Two-step silane cross-linked polyethylene insulation production process
The production process of the two-step silane cross-linked polyethylene insulation A material can be briefly represented by Figure 1.
Figure 1 Production process of two-step silane cross-linked polyethylene insulating material A
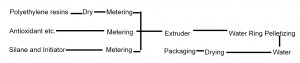
Some key points in the production process of two-step silane cross-linked polyethylene insulation:
(1) Drying. As the polyethylene resin contains a small amount of water, when extruded at high temperatures, the water reacts rapidly with the silyl groups to produce cross-linking, which reduces the fluidity of the melt and produces pre-cross-linking. The finished material also contains water after water cooling, which can also cause pre-crosslinking if not removed, and must also be dried. In order to ensure the quality of the drying, a deep drying unit is used.
(2) Metering. As the accuracy of the material formulation is important, an imported loss-in-weight weighing scale is generally used. The polyethylene resin and antioxidant are measured and fed through the feed port of the extruder, while the silane and initiator are injected by a liquid material pump in the second or third barrel of the extruder.
(3) Extrusion grafting. The grafting process of silane is completed in the extruder. The process settings of the extruder, including temperature, screw combination, screw speed and feed rate, must follow the principle that the material in the first section of the extruder can be fully molten and mixed uniformly, when premature decomposition of the peroxide is not desired, and that the fully uniform material in the second section of the extruder must be fully decomposed and the grafting process completed, Typical extruder section temperatures (LDPE) are shown in Table 1.
Table 1 Temperatures of the two-step extruder zones
Working zone | Zone 1 | Zone 2 | Zone 3 ① | Zone 4 | Zone 5 |
Temperature P °C | 140 | 145 | 120 | 160 | 170 |
Working zone | Zone 6 | Zone 7 | Zone 8 | Zone 9 | Mouth die |
Temperature °C | 180 | 190 | 195 | 205 | 195 |
①is where the silane is added.
The speed of the extruder screw determines the residence time and the mixing effect of the material in the extruder, if the residence time is short, the peroxide decomposition is incomplete; if the residence time is too long, the viscosity of the extruded material increases. In general, the average residence time of the granule in the extruder should be controlled in the initiator decomposition half-life of 5-10 times. Feeding speed not only has a certain impact on the residence time of the material, but also on the mixing and shearing of the material, choose an appropriate feeding speed is also very important.
(4) Packaging. Two-step silane cross-linked insulating material should be packaged in aluminium-plastic composite bags in direct air to eliminate moisture.
5. One-step silane cross-linked polyethylene insulating material production process
One-step silane cross-linked polyethylene insulation material because of its grafting process is in the cable factory extrusion of cable insulation core, so the cable insulation extrusion temperature is significantly higher than the two-step method. Although the one-step silane cross-linked polyethylene insulation formula has been fully considered in the rapid dispersion of initiator and silane and material shear, but the grafting process must be guaranteed by the temperature, which is the one-step silane cross-linked polyethylene insulation production plant repeatedly stressed the importance of the correct choice of extrusion temperature, the general recommended extrusion temperature is shown in Table 2.
Table 2 One-step extruder temperature of each zone ( unit: ℃ )
Zone | Zone 1 | Zone 2 | Zone 3 | Zone 4 | Flange | Head |
Temperature | 160 | 190 | 200~210 | 220~230 | 230 | 230 |
This is one of the weaknesses of the one-step silane cross-linked polyethylene process, which is generally not required when extruding cables in two steps.
6.Production equipment
The production equipment is an important guarantee of process control. The production of silane cross-linked cables requires a very high degree of process control accuracy, so the choice of production equipment is particularly important.
The production of two-step silane cross-linked polyethylene insulation material A material production equipment, currently more domestic isotropic parallel twin-screw extruder with imported weightless weighing, such devices can meet the requirements of process control accuracy, the choice of length and diameter of the twin-screw extruder to ensure that the material residence time, the choice of imported weightless weighing to ensure the accuracy of the ingredients. Of course there are many details of the equipment that need to be given full attention.
As mentioned earlier, the one-step silane cross-linked cable production equipment in the cable plant are imported, expensive, domestic equipment manufacturers do not have similar production equipment, the reason is the lack of cooperation between equipment manufacturers and formula and process researchers.
7.Silane natural cross-linked polyethylene insulation material
Silane natural cross-linked polyethylene insulating material developed in recent years can be cross-linked under natural conditions within a few days, without steam or warm water immersion. Compared with the traditional silane cross-linking method, this material can reduce the production process for cable manufacturers, further reducing production costs and increasing production efficiency. Silane naturally cross-linked polyethylene insulation is increasingly recognised and used by cable manufacturers.
In recent years, domestic silane natural cross-linked polyethylene insulation has matured and has been produced in large quantities, with certain advantages in price compared to imported materials.
7. 1 Formulation ideas for silane naturally cross-linked polyethylene insulations
Silane natural cross-linked polyethylene insulations are produced in a two-step process, with the same formulation consisting of base resin, initiator, silane, antioxidant, polymerisation inhibitor and catalyst. The formulation of silane natural cross-linked polyethylene insulators is based on increasing the silane grafting rate of the A material and selecting a more efficient catalyst than silane warm water cross-linked polyethylene insulators. The use of A materials with a higher silane grafting rate combined with a more efficient catalyst will enable the silane cross-linked polyethylene insulator to cross-link quickly even at low temperatures and with insufficient moisture.
The A-materials for imported silane naturally cross-linked polyethylene insulators are synthesised by copolymerisation, where the silane content can be controlled at a high level, whereas the production of A-materials with high grafting rates by grafting silane is difficult. The base resin, initiator and silane used in the recipe should be varied and adjusted in terms of variety and addition.
The selection of the resist and the adjustment of its dosage are also crucial, as an increase in the grafting rate of the silane inevitably leads to more C-C crosslinking side reactions. In order to improve the processing fluidity and surface condition of the A material for subsequent cable extrusion, a suitable amount of polymerization inhibitor is required to effectively inhibit C-C crosslinking and prior pre-crosslinking.
In addition, catalysts play an important role in increasing the crosslinking rate and should be selected as efficient catalysts containing transition metal-free elements.
7. 2 Crosslinking time of silane naturally crosslinked polyethylene insulations
The time required to complete the cross-linking of silane natural cross-linked polyethylene insulation in its natural state is dependent on the temperature, humidity and thickness of the insulation layer. The higher the temperature and humidity, the thinner the thickness of the insulation layer, the shorter the crosslinking time required, and the longer the opposite. As the temperature and humidity vary from region to region and from season to season, even in the same place and at the same time, the temperature and humidity today and tomorrow will be different. Therefore, during the use of the material, the user should determine the cross-linking time according to the local and prevailing temperature and humidity, as well as the specification of the cable and the thickness of the insulation layer.
Post time: Aug-13-2022