The basic structure of wire and cable includes conductor, insulation, shielding, sheath and other parts.

1. Conductor
Function: Conductor is a component of a wire and cable that transmits electrical (magnetic) energy, information and realizes specific functions of electromagnetic energy conversion.
Material: There are mainly uncoated conductors, such as copper, aluminum, copper alloy, aluminum alloy; metal-coated conductors, such as tinned copper, silver-plated copper, nickel-plated copper; metal-clad conductors, such as copper-clad steel, copper-clad aluminum, aluminum clad steel, etc.
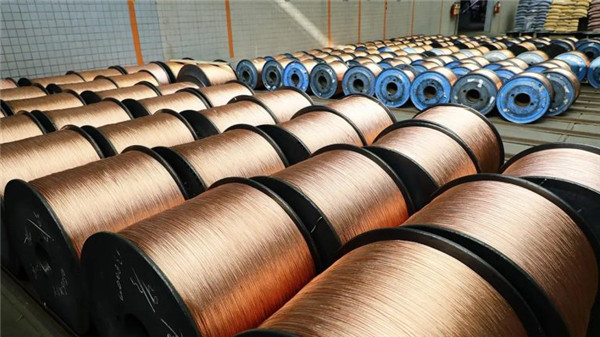
2. Insulation
Function: The insulating layer is wrapped around the conductor or the additional layer of the conductor (such as refractory mica tape), and its function is to isolate the conductor from bearing the corresponding voltage and prevent leakage current.
The commonly used materials for extruded insulation are polyvinyl chloride (PVC), polyethylene (PE), cross-linked polyethylene (XLPE), low-smoke halogen-free flame retardant polyolefin (LSZH/HFFR), fluoroplastics, thermoplastic elasticity (TPE), silicone rubber (SR), ethylene propylene rubber (EPM/EPDM), etc.
3. Shielding
Function: The shielding layer used in wire and cable products actually has two completely different concepts.
First, the structure of wires and cables that transmit high-frequency electromagnetic waves (such as radio frequency, electronic cables) or weak currents (such as signal cables) is called electromagnetic shielding. The purpose is to block the interference of external electromagnetic waves, or to prevent the high-frequency signals in the cable from interfering with the outside world, and to prevent mutual interference between wire pairs.
Second, the structure of medium and high voltage power cables to equalize the electric field on the conductor surface or the insulating surface is called electric field shielding. Strictly speaking, the electric field shielding does not require the function of “shielding”, but only plays the role of homogenizing the electric field. The shield that wraps around the cable is usually grounded.
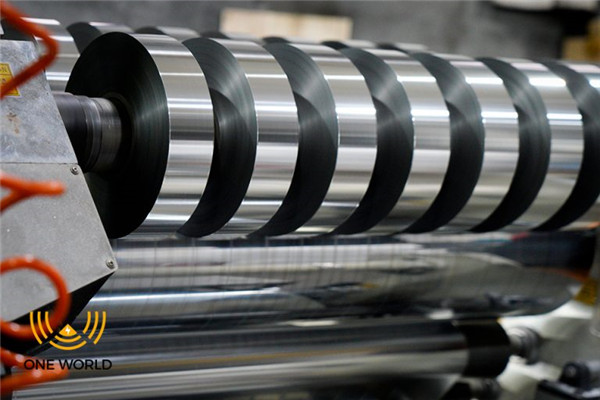
* Electromagnetic shielding structure and materials
① Braided shielding: mainly use bare copper wire, tin-plated copper wire, silver-plated copper wire, aluminum-magnesium alloy wire, copper flat tape, silver-plated copper flat tape, etc. to be braided outside the insulated core, wire pair or cable core;
② Copper tape shielding: use soft copper tape to cover or wrap vertically outside the cable core;
③ Metal composite tape shielding: use aluminum foil Mylar tape or copper foil Mylar tape to wrap around or vertically wrap the wire pair or cable core;
④ Comprehensive shielding: Comprehensive application by different forms of shielding.For example, wrap (1-4) thin copper wires vertically after wrapping with aluminum foil Mylar tape. The copper wires can increase the conduction effect of the shielding;
⑤ Separate shielding + overall shielding: each wire pair or group of wires is shielded by aluminum foil Mylar tape or copper wire braided separately, and then the overall shielding structure is added after cabling;
⑥ Wrapping shielding: Use thin copper wire, copper flat tape, etc. to wrap around the insulated wire core, wire pair or cable core.
* Electric field shielding structure and materials
Semi-conductive shielding: For power cables of 6kV and above, a thin semi-conductive shielding layer is attached to the conductor surface and the insulating surface. The conductor shielding layer is an extruded semi-conductive layer. Conductor shielding with a cross-section of 500mm² and above is generally composed of semi-conductive tape and extruded semi-conductive layer. The insulating shielding layer is extruded structure;
Copper wire wrapping: The round copper wire is mainly used for co-directional wrapping, and the outer layer is reversely wound and fastened with copper tape or copper wire. This type of structure is usually used in cables with large short-circuit current, such as some large-section 35kV cables. single-core power cable;
Copper tape wrapping: wrapping with soft copper tape;
④ Corrugated aluminum sheath: It adopts hot extrusion or aluminum tape longitudinal wrapping, welding, embossing, etc. This type of shielding also has excellent water-blocking, and is mainly used for high-voltage and ultra-high-voltage power cables.
4. Sheath
The function of the sheath is to protect the cable, and the core is to protect the insulation. Due to the ever-changing usage environment, usage conditions and user requirements. Therefore, the types, structural forms and performance requirements of the sheathing structure are also varied, which can be summarized into three categories:
One is to protect the external climatic conditions, occasional mechanical forces, and a general protective layer that requires general sealing protection (such as preventing the intrusion of water vapor and harmful gases); If there is a large mechanical external force or bear the weight of the cable, there must be a protective layer structure of the metal armor layer; the third is the protective layer structure with special requirements.
Therefore, the sheath structure of wire and cable is generally divided into two major components: sheath (sleeve) and outer sheath. The structure of the inner sheath is relatively simple, while the outer sheath includes the metal armor layer and its inner lining layer (to prevent the armor layer from damaging the inner sheath layer), and the outer sheath which is to protect armor layer, etc. For a variety of special requirements such as flame retardant, fire resistance, anti-insect (termite), anti-animal (rat bite, bird peck), etc., most of them are solved by adding various chemicals to the outer sheath; a few must add necessary components in the outer sheath structure..
Commonly used materials are:
Polyvinyl chloride (PVC), polyethylene (PE), polyperfluoroethylene propylene (FEP), low smoke halogen free flame retardant polyolefin (LSZH/HFFR), thermoplastic elastomer (TPE)
Post time: Dec-30-2022