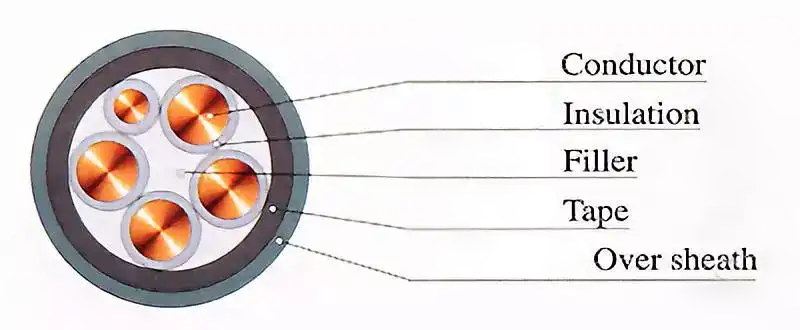
The structural components of wire and cable products can be generally divided into four main parts: conductors, insulation layers, shielding and protective layers, along with filling components and tensile elements. According to the usage requirements and application scenarios, some product structures are quite simple, having only conductors as a structural component, such as overhead bare wires, contact network wires, copper-aluminum busbars (busbars), etc. The external electrical insulation of these products relies on insulators during installation and spatial distance (i.e., air insulation) to ensure safety.
1. Conductors
Conductors are the most fundamental and indispensable components responsible for the transmission of electric current or electromagnetic wave information within a product. Conductors, often referred to as conductive wire cores, are made from high-conductivity non-ferrous metals like copper, aluminum, etc. Fiber optic cables used in rapidly evolving optical communication networks over the last thirty years employ optical fibers as conductors.
2. Insulation Layers
These components envelop the conductors, providing electrical insulation. They ensure that the current or electromagnetic/optical waves transmitted only travel along the conductor and not outward. Insulation layers maintain the potential (i.e., voltage) on the conductor from influencing surrounding objects and ensuring both the normal transmission function of the conductor and external safety for objects and people.
Conductors and insulation layers are the two fundamental components necessary for cable products (except for bare wires).
In various environmental conditions during installation and operation, wire and cable products must have components that offer protection, especially for the insulation layer. These components are known as protective layers.
Because insulation materials must possess excellent electrical insulation properties, they require high purity with minimal impurity content. However, these materials often cannot simultaneously provide protection from external factors (i.e., mechanical forces during installation and use, resistance to atmospheric conditions, chemicals, oils, biological threats, and fire hazards). These requirements are handled by various protective layer structures.
For cables designed specifically for favorable external environments (e.g., clean, dry, indoor spaces without external mechanical forces), or in cases where the insulation layer material itself exhibits certain mechanical strength and climate resistance, there might be no requirement for a protective layer as a component.
4. Shielding
It's a component in cable products that isolates the electromagnetic field within the cable from external electromagnetic fields. Even among different wire pairs or groups within cable products, mutual isolation is necessary. The shielding layer can be described as an "electromagnetic isolation screen."
For many years, the industry has regarded the shielding layer as a part of the protective layer structure. However, it's proposed that it should be considered as a separate component. This is because the function of the shielding layer is not only to electromagnetically isolate the information transmitted within the cable product, preventing it from leaking or causing interference to external instruments or other lines, but also to prevent external electromagnetic waves from entering the cable product through electromagnetic coupling. These requirements differ from traditional protective layer functions. Additionally, the shielding layer is not only set externally in the product but also placed between each wire pair or multiple pairs in a cable. Over the past decade, due to the rapid development of information transmission systems using wires and cables, along with an increasing number of electromagnetic wave interference sources in the atmosphere, the variety of shielded structures has multiplied. The understanding that the shielding layer is a fundamental component of cable products has become widely accepted.
Many wire and cable products are multi-core, such as most low-voltage power cables being four-core or five-core cables (suitable for three-phase systems), and urban telephone cables ranging from 800 pairs to 3600 pairs. After combining these insulated cores or wire pairs into a cable (or multiple times grouping), irregular shapes and large gaps exist between the insulated cores or wire pairs. Therefore, a filling structure must be incorporated during cable assembly. The purpose of this structure is to maintain a relatively uniform outer diameter in coiling, facilitating wrapping and sheath extrusion. Moreover, it ensures cable stability and internal structure integrity, distributing forces evenly during use (stretching, compression, and bending during manufacturing and laying) to prevent damage to the cable's internal structure.
Therefore, although the filling structure is auxiliary, it's necessary. Detailed regulations exist regarding the material selection and design of this structure.
Traditional wire and cable products typically rely on the armored layer of the protective layer to withstand external tensile forces or the tension caused by their own weight. Typical structures include steel tape armoring and steel wire armoring (such as using 8mm thick steel wires, twisted into an armored layer, for submarine cables). However, in optical fiber cables, to protect the fiber from minor tensile forces, avoiding any slight deformation that might affect transmission performance, primary and secondary coatings and specialized tensile components are incorporated into the cable structure. For instance, in mobile phone headset cables, a fine copper wire or thin copper tape wound around synthetic fiber is extruded with an insulating layer, where the synthetic fiber acts as a tensile component. Overall, in recent years, in the development of special small and flexible products that require multiple bends and twists, tensile elements play a significant role.
Post time: Dec-19-2023