1 Introduction
To ensure the longitudinal sealing of fiber optic cables and to prevent water and moisture from penetrating into the cable or junction box and corroding the metal and fiber, resulting in hydrogen damage, fiber breakage and a sharp drop in electrical insulation performance, the following methods are commonly used to prevent water and moisture:
1) Filling the inside of the cable with thixotropic grease, including water-repellent (hydrophobic) type, water swelling type and heat expansion type and so on. This type of material are oily materials, filling a large amount, high cost, easy to pollute the environment, difficult to clean (especially in the cable splicing with the solvent to clean), and the cable’s self-weight too heavy.
2) In the inner and outer sheath between the use of hot melt adhesive water barrier ring, this method is inefficient, complex process, only a few manufacturers can achieve. 3) The use of dry expansion of water-blocking materials (water-absorbing expansion powder, water-blocking tape, etc.). This method requires high technology, material consumption, high cost, the self-weight of the cable is also too heavy. In recent years, the “dry core” structure has been introduced into the optical cable, and has been well applied abroad, especially in solving the problem of heavy self-weight and complex splicing process of large core number of optical cable has incomparable advantages. The water-blocking material used in this “dry core” cable is water-blocking yarn. The water-blocking yarn can quickly absorb water and swell to form a gel, blocking the space of the cable’s water channel, thus achieving the purpose of water blocking. In addition, the water-blocking yarn contains no oily substances and the time required to prepare the splice can be reduced considerably without the need for wipes, solvents and cleaners. In order to obtain a simple process, convenient construction, reliable performance and low cost water-blocking materials, we developed a new type of optical cable water-blocking yarn-water-blocking swellable yarn.
2 Water blocking principle and characteristics of the water blocking yarn
The water-blocking function of water-blocking yarn is to use the main body of the water-blocking yarn fibers to form a large volume of gel (water absorption can reach dozens of times its own volume, such as in the first minute of water can be rapidly expanded from about 0. 5mm to about 5. 0mm diameter), and the water retention capacity of the gel is quite strong, can effectively prevent the growth of the water tree, thus preventing water from continuing to penetrate and spread, to achieve The purpose of water resistance. As fiber optic cable must withstand various environmental conditions during manufacture, testing, transportation, storage and use, water-blocking yarn must have the following characteristics to be used in fiber optic cable:
1) A clean appearance, uniform thickness and a soft texture;
2) A certain mechanical strength to meet the tension requirements when forming the cable;
3) fast swelling, good chemical stability and high strength for water absorption and gel formation;
4) Good chemical stability, no corrosive components, resistant to bacteria and moulds;
5) Good thermal stability, good weather resistance, adaptable to various subsequent processing and production and various use environments;
6) Good compatibility with other materials of fiber optic cable.
3 Water-resistant yarn in the application of optical fiber cable
3.1 The use of water-resistant yarns in optical fiber cables
Fiber optic cable manufacturers can adopt different cable structures in the production process to meet the needs of users according to their actual situation and the requirements of users:
1) Longitudinal water blocking of the outer sheath with water-blocking yarns
In wrinkled steel tape armouring, the outer sheath must be longitudinally waterproof to prevent moisture and humidity from entering the cable or the connector box. In order to achieve the longitudinal water barrier of the outer sheath, two water barrier yarns are used, one of which is placed parallel to the inner sheath cable core, and the other is wrapped around the cable core at a certain pitch (8 to 15 cm), covered with wrinkled steel tape and PE (polyethylene), so that the water barrier yarn divides the gap between the cable core and the steel tape into a small closed compartment. The water barrier yarn will swell and form a gel within a short time, preventing the water from entering the cable and restricting the water to a few small compartments near the fault point, thus achieving the purpose of longitudinal water barrier, as shown in Figure 1.
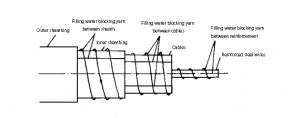
Figure 1: Typical usage of water blocking yarn in optical cable
2) Longitudinal water blocking of the cable core with water-blocking yarnsCan be used in the cable core of two parts of the water-blocking yarn, one is in the cable core of the reinforced steel wire, using two water-blocking yarn, usually a water-blocking yarn and reinforced steel wire placed in parallel, another water-blocking yarn to a larger pitch wrapped around the wire, there are also two water-blocking yarn and reinforced steel wire placed in parallel, the use of water-blocking yarn of strong expansion capacity to block water; second is in the loose casing surface, before squeezing the inner sheath, the water-blocking yarn as a tie yarn use, two water-blocking yarn to a smaller pitch ( 1 ~ 2cm) in the opposite direction around, forming a dense and small blocking bin, to prevent the entry of water, made of “dry cable core” structure.
3.2 Selection of water resistant yarns
In order to obtain both good water resistance and satisfactory mechanical processing performance in the manufacturing process of fiber optic cable, the following aspects should be noted when selecting water resistance yarn:
1) The thickness of the water-blocking yarn
In order to ensure that the expansion of the water-blocking yarn can fill the gap in the cross-section of the cable, the choice of the thickness of the water-blocking yarn is crucial, of course, this is related to the structural size of the cable and the expansion rate of the water-blocking yarn. In the cable structure should minimize the existence of gaps, such as the use of high expansion rate of the water-blocking yarn, then the diameter of the water-blocking yarn can be reduced to the smallest, so that you can obtain reliable water-blocking performance, but also to save costs.
2) Swelling rate and gel strength of water-blocking yarns
IEC794-1-F5B water penetration test is carried out on the full cross-section of the fiber optic cable. 1m of water column is added to a 3m sample of fiber optic cable, 24h without leakage is qualified. If the swelling rate of the water-blocking yarn does not keep up with the rate of water infiltration, it is possible that the water has passed through the sample within a few minutes of starting the test and the water-blocking yarn has not yet fully swelled, although after a period of time the water-blocking yarn will fully swell and block the water, but this is also a failure. If the expansion rate is faster and the gel strength is not enough, it is not enough to resist the pressure generated by the 1m water column, and the water blocking will also fail.
3) Softness of the water-blocking yarn
As the softness of the water-blocking yarn on the mechanical properties of the cable, especially the lateral pressure, impact resistance, etc., the impact is more obvious, so should try to use a more soft water-blocking yarn.
4) The tensile strength, elongation and length of the water-blocking yarn
In the production of each cable tray length, water-blocking yarn should be continuous and uninterrupted, which requires water-blocking yarn must have a certain tensile strength and elongation, in order to ensure that the water-blocking yarn is not pulled during the production process, the cable in the case of stretching, bending, twisting water-blocking yarn is not damaged. The length of the water-blocking yarn depends mainly on the length of the cable tray, in order to reduce the number of times the yarn is changed in continuous production, the longer the length of the water-blocking yarn the better.
5) The acidity and alkalinity of the water-blocking yarn should be neutral, otherwise the water-blocking yarn will react with the cable material and precipitate hydrogen.
6) Stability of water-blocking yarns
Table 2: Comparison of the water-blocking structure of water-blocking yarns with other water-blocking materials
Compare items | Jelly filling | Hot melt water stopper ring | Water blocking tape | Water blocking yarn |
Water resistance | Good | Good | Good | Good |
Processability | Simple | Complicated | More complex | Simple |
Mechanical properties | Qualified | Qualified | Qualified | Qualified |
Long-term reliability | Good | Good | Good | Good |
Sheath bonding force | Fair | Good | Fair | Good |
Connection risk | Yes | No | No | No |
Oxidation effects | Yes | No | No | No |
Solvent | Yes | No | No | No |
Mass per unit length of fibre optic cable | Heavy | Light | Heavier | Light |
Unwanted material flow | Possible | No | No | No |
Cleanliness in production | Poor | More poor | Good | Good |
Material handling | Heavy iron drums | Simple | Simple | Simple |
Investment in equipment | Large | Large | Larger | Small |
Material cost | Higher | Low | Higher | Lower |
Production costs | Higher | Higher | Higher | Lower |
The stability of water-blocking yarns is mainly measured by short-term stability and long-term stability. Short-term stability is mainly considered short-term temperature rise (extrusion sheath process temperature up to 220 ~ 240 ° C) on the water barrier yarn water barrier properties and mechanical properties of the impact; long-term stability, mainly considering the aging of the water barrier yarn expansion rate, expansion rate, gel strength and stability, tensile strength and elongation of the impact, the water barrier yarn must be in the cable’s entire life ( 20 ~ 30 years) are Water resistance. Similar to water-blocking grease and water-blocking tape, the gel strength and stability of the water-blocking yarn is an important characteristic. A water-blocking yarn with high gel strength and good stability can maintain good water-blocking properties for a considerable period of time. On the contrary, according to the relevant German national standards, some materials under hydrolysis conditions, the gel will decompose into a very mobile low molecular weight material, and will not achieve the purpose of long-term water resistance.
3.3 Application of water-blocking yarns
Water-blocking yarn as an excellent optical cable water-blocking materials, is replacing the oil paste, hot melt adhesive water-blocking ring and water-blocking tape, etc. used in large quantities in the production of optical cable, Table 2 on some of the characteristics of these water-blocking materials for comparison.
4 Conclusion
In summary, the water-blocking yarn is an excellent water-blocking material suitable for optical cable, it has the characteristics of simple construction, reliable performance, high production efficiency, easy to use; and the use of the material filling the optical cable has the advantages of light weight, reliable performance and low cost.
Post time: Jul-16-2022